The Early Inspiration Behind Bluepoint Tags & Labels
Rob Burton and Iain Pringle have been working together for more than 30 years making specialist tags and labels.
Before setting up Bluepoint Tags and Labels, Rob and Iain helped to establish and develop Longcombe Labels based in South Devon. When that was taken over by a conglomerate in 2014 their ambition to run their own company came into sharp focus. Their experience and passion for the industry was there and they knew that given the chance they could do things differently. In 2017 they seized that opportunity to set up on their own and Bluepoint was born. Winding forwards several years, they now have a thriving business in Totnes with a turnover of around £3m and a driven team who describe Bluepoint more as “a family than a place of work”.
A Promising Start
Their first press was a second-hand Mark Andy 2200 press, a trusted and well-known friend, meaning they could hit the ground running, and was joined by a second press just a year later. A thorough knowledge of these machines meant that they could do their own repairs and maintenance so down time was limited. The nature of their work is highly specialised – the manufacture of unsupported tags for use in harsh and demanding environments, initially relying on a variety of plastic substrates, but now looking at more sustainable, eco-friendly alternatives.
The barriers to entry in this industry are high: machines and presses are very expensive, tooling costs run well into four figures and difficulties around perforating and punching and waste removal can lead to expensive material losses. This is where their experience came to the fore. Obviously, in the early days with mortgages and young families to support, there were nervous times, but with a strong emphasis on customer service and a hunger to problem solve, the snowball began to roll.
Bluepoint began in a unit on the industrial estate at Exeter Airport, fondly known as the “Tin Shed”. Within a year, growth was such that they had to rent another unit for the storage of materials and by 2019 they had moved into a 4,000 square foot factory in Totnes where they had started out nearly 30 years earlier.
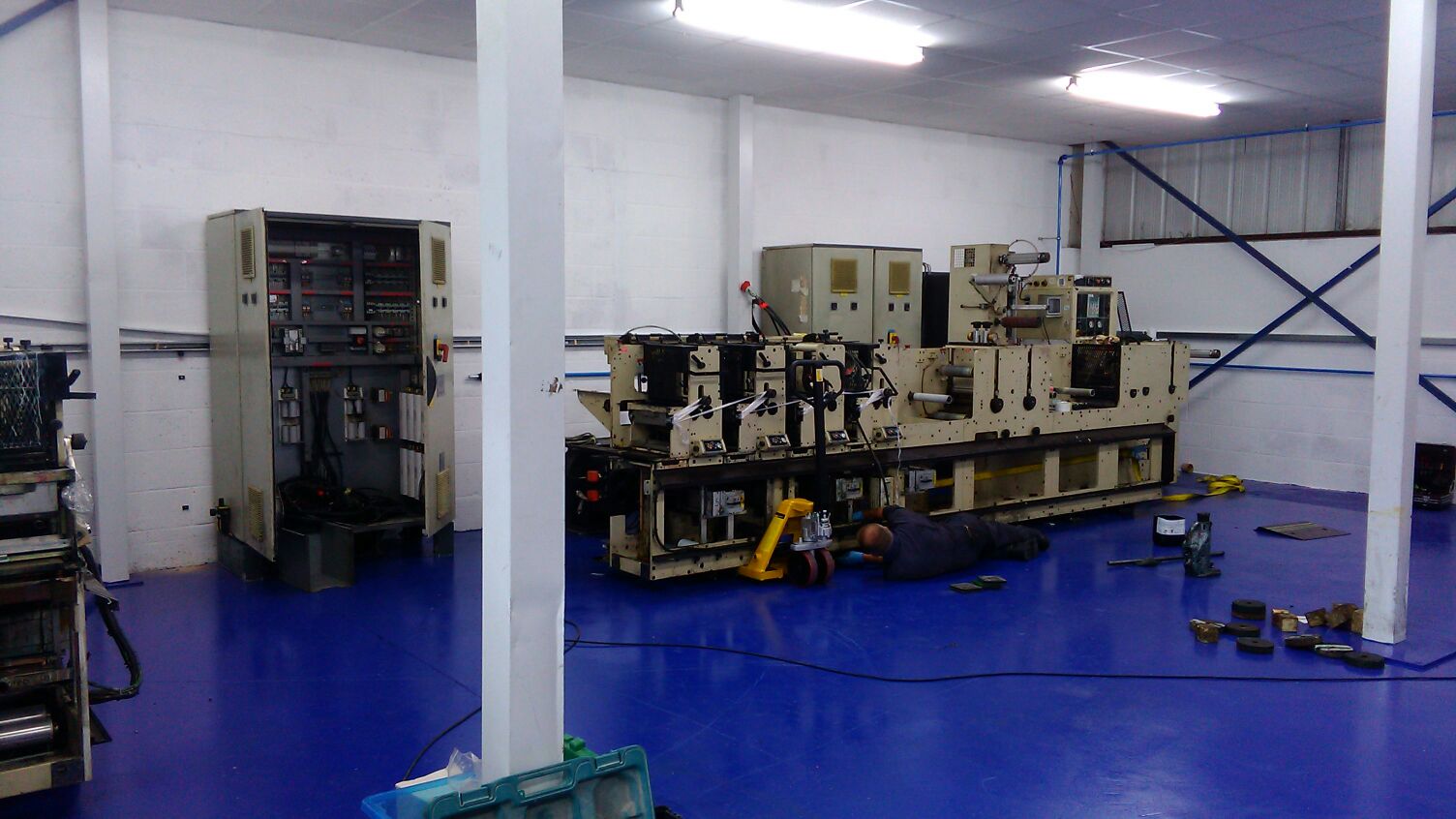
The Drive For Growth
The rapid growth in the company has come about for three main reasons. Firstly, an insistence on first class customer service in every respect. Bluepoint work to build solid relationships not only with their customers, but also with their suppliers, and they put real value in this.
Secondly, Bluepoint are dedicated to the production of quality products. With an emphasis on manufacturing industry-leading products, they are constantly looking to source innovative new (and where possible, sustainable) materials and to invest in new machinery and tooling to support the business and their customers; 2024 saw the arrival of a semi-automatic turret rewind machine – increasing both production efficiencies and output.
Thirdly, Bluepoint demonstrate a willingness to work on new product development with customers, something that is very important for the business. Bluepoint does much work for trade houses and end users who are keen to use the experience of the team at Bluepoint to drive innovation.
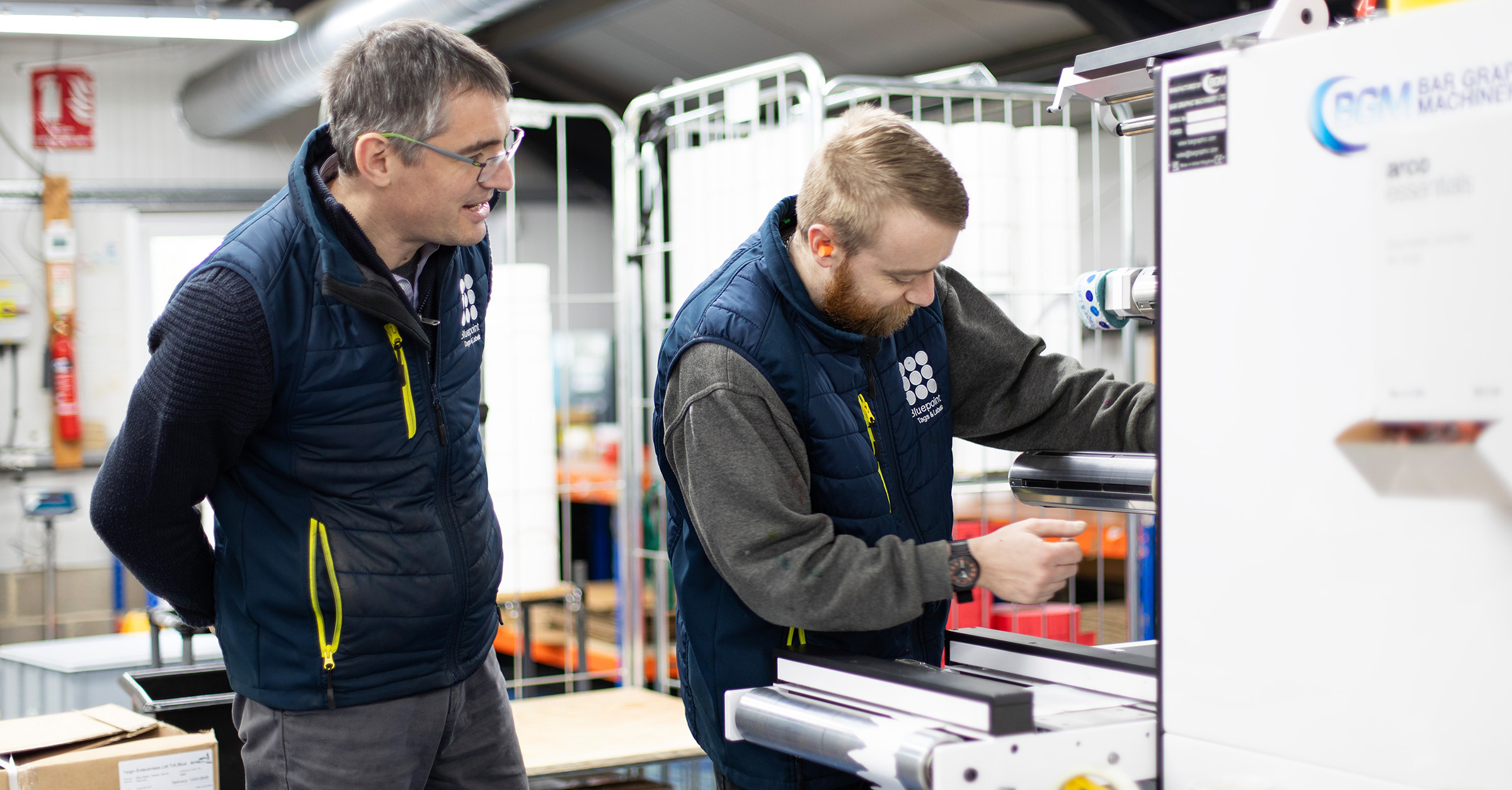
New Investment
By the time of their 2019 move to Totnes, Bluepoint had started to establish a name for themselves as manufacturers of tough tags for tough environments, for example, in steel, construction, horticulture and food production. Once they had settled into their new Totnes base, and with a growing in interest in the Bluepoint brand, Iain and Rob decided to invest in further machinery - acquiring a third complete press.
However, this press was bought and paid for on the day the Covid restrictions were declared, and although Bluepoint continued to trade and support their customers throughout the pandemic, installers weren’t available to commission the new press until later that year, and it wasn’t until early 2021 that this new production line was fully up to speed - just in time to meet an unprecedented demand that far exceeded pre-pandemic levels.
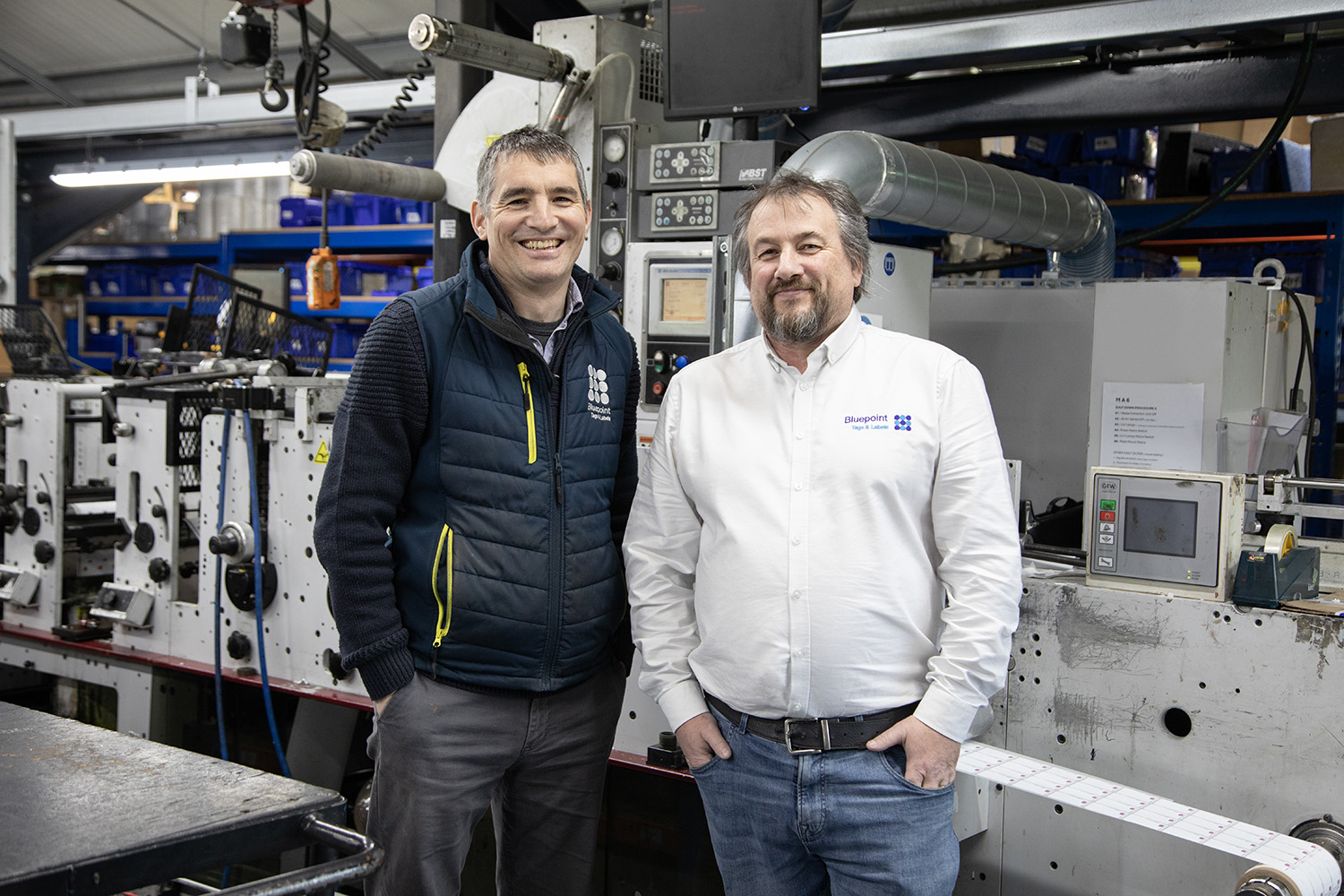
Moving Towards Sustainable Practices
Bluepoint is aware of the need for sustainability in all that they do and understand that the industrial labelling sector relies heavily on synthetic materials and plastics, and as such, they strive constantly to involve recycled and recyclable materials in their production. Their wristbands can be made in litter free form or, with their new Recyclaband product, made from a PVC-free, sustainably sourced, paper-based stock.
To counter the use of synthetic materials, Bluepoint have, for a long time, been looking to reduce their own impact on the environment; although there are many carbon offsetting schemes available to businesses, Iain and Rob chose to make a real difference here at the factory, and in 2024, solar panels were installed on the factory roof. By its nature as a manufacturer, Bluepoint is a heavy energy user, and although the very recent installation (think a dark, wet, Devon winter) means that the actual savings are hard to quantify yet, they have already seen a reduction in their energy use, and are excited to see the true benefit once they move towards summer.
Since the installation in late October 2024, around 10% of the daily electricity use has been provided by the solar panels, with 2.83 MWh being generated in the last three months alone. That equates to a CO2 saving of 608.1kg so far - the equivalent to planting 37 trees! Sunny summer days are projected to give 100% of energy use coming from Bluepoint’s own solar generated electricity, with around 20% of the power created going back into the grid. It’s estimated that the total annual electricity use from the grid will be reduced by up to 40%.
Further to the installation of solar panels, the lighting throughout the factory has been converted to low-energy LED, EV charging points have just been installed and 2025 sees all company vehicles switching to EV – charged with electricity that Bluepoint have generated themselves.
Bluepoint feels that ‘every little helps’ and is driven to ensure that they lower their carbon footprint as much as possible, wherever possible. Further to being more environmentally responsible, there is a cost saving that comes with generating their own electricity, and this benefit can then be passed onto their customers.
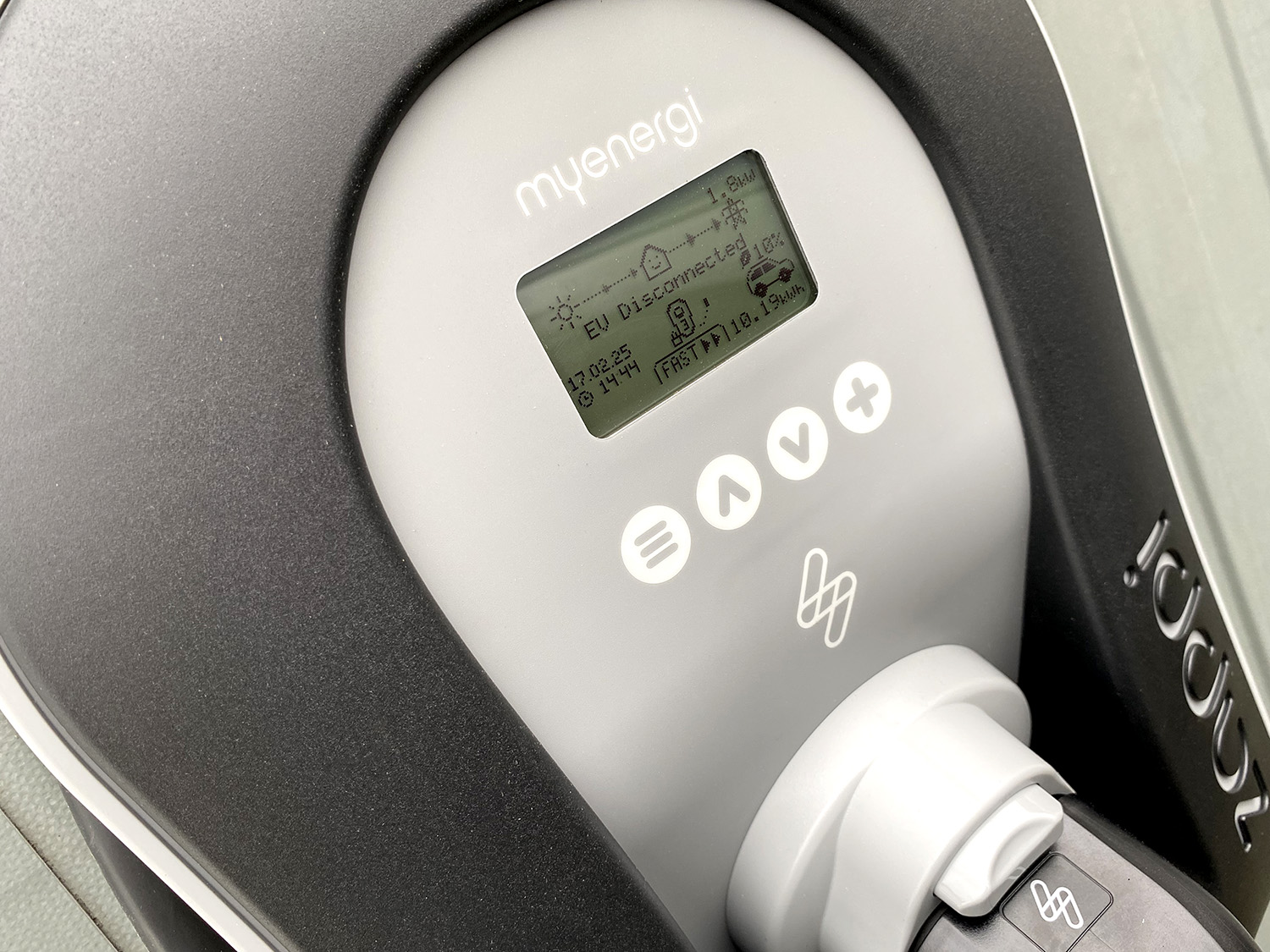
Moving To The Future
Future plans for Bluepoint include the expansion of their reseller base, continuing growth in their export sales, the appointment of overseas agents and the development of more innovative products.
The single Mark Andy 2200 now has four siblings, the packing and rewinding section has brand new equipment installed and the ‘two kids in a tin shed’ now have a dozen playmates all happily making first class products in their niche market.
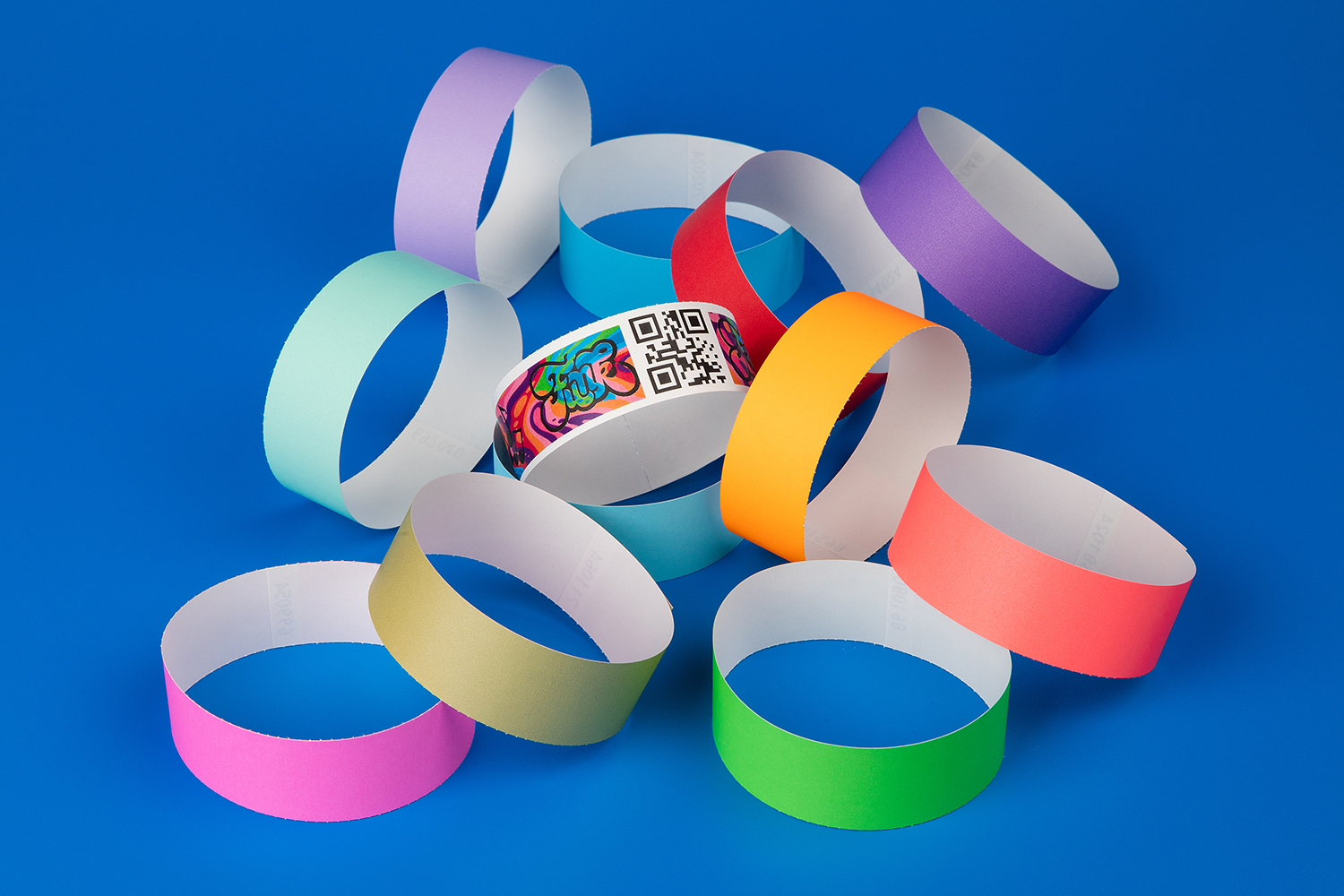