How Bluepoint Tags is Improving Forklift Safety in the Workplace
As with many UK manufacturers, a forklift is a vital piece of equipment here at Bluepoint and is used by staff here at our factory on a daily basis. This January, three of our team took part in a programme of workplace health and safety training in the correct use of a forklift – not only is this a legal requirement under the Health and Safety at Work Act, but it also comes with several benefits for a small manufacturer such as ourselves. To find out why, read on...!
Why Do We Need Forklift Training?
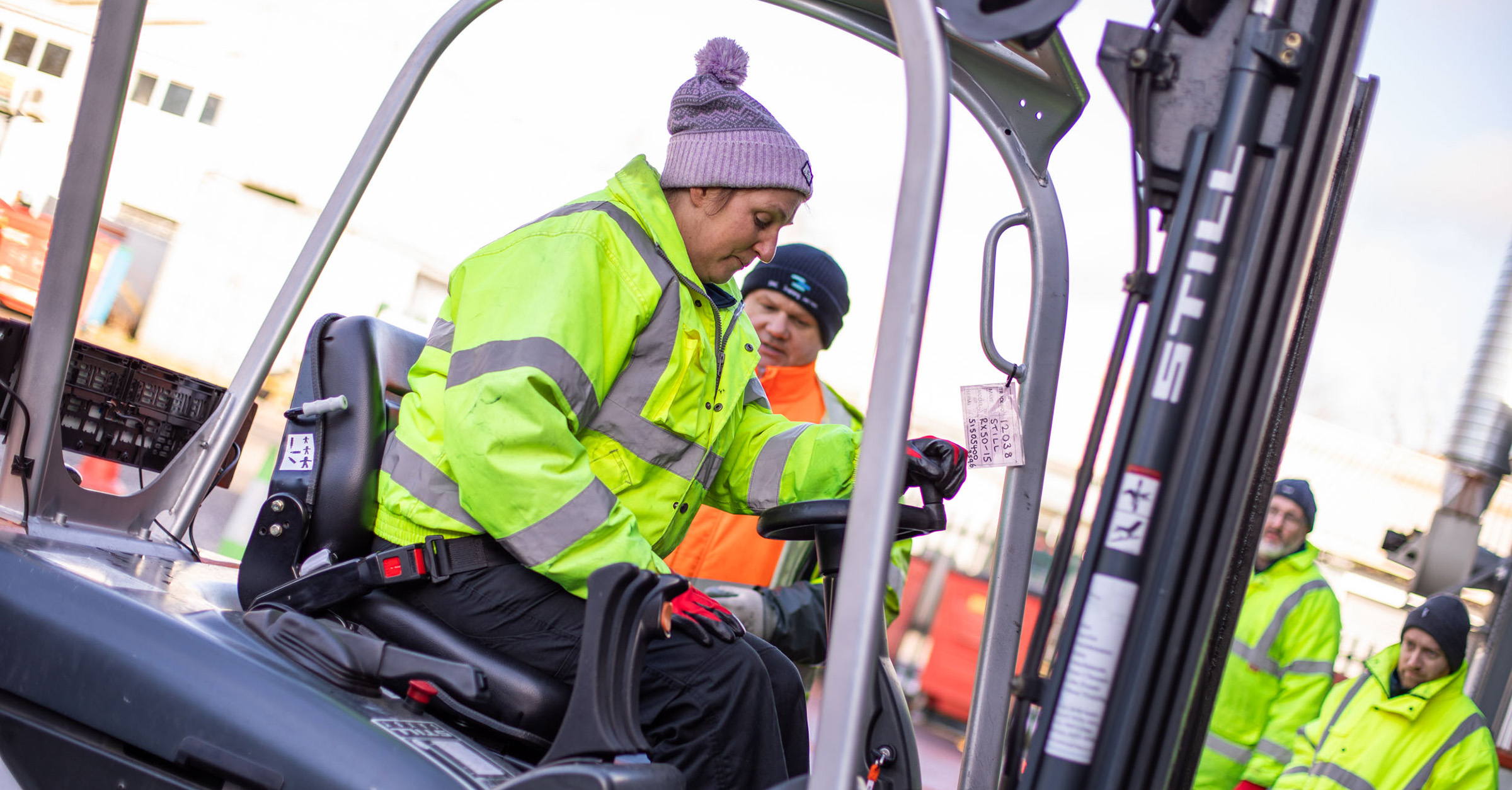
Aside from the legal requirement, forklifts can be tricky things to drive, so it’s important that our team have the relevant training.
For instance, most forklifts are rear steer, which is great for manoeuvring in tight spaces, but can be tricky to get used to if you’ve only ever driven a car. Then comes training on the basic functions such as working the brakes and accelerator, using the warning lights and horn, and operating the forks themselves.
Perhaps more important is understanding the fact that a forklift is designed to carry a heavy load, and an operator needs to know how the forklift behaves when it’s loaded, as well as correct procedures for loading and unloading – at the very least a dropped load will mean damage to your product, worse still, an injury to yourself or other team members.
Other Benefits of Forklift Training
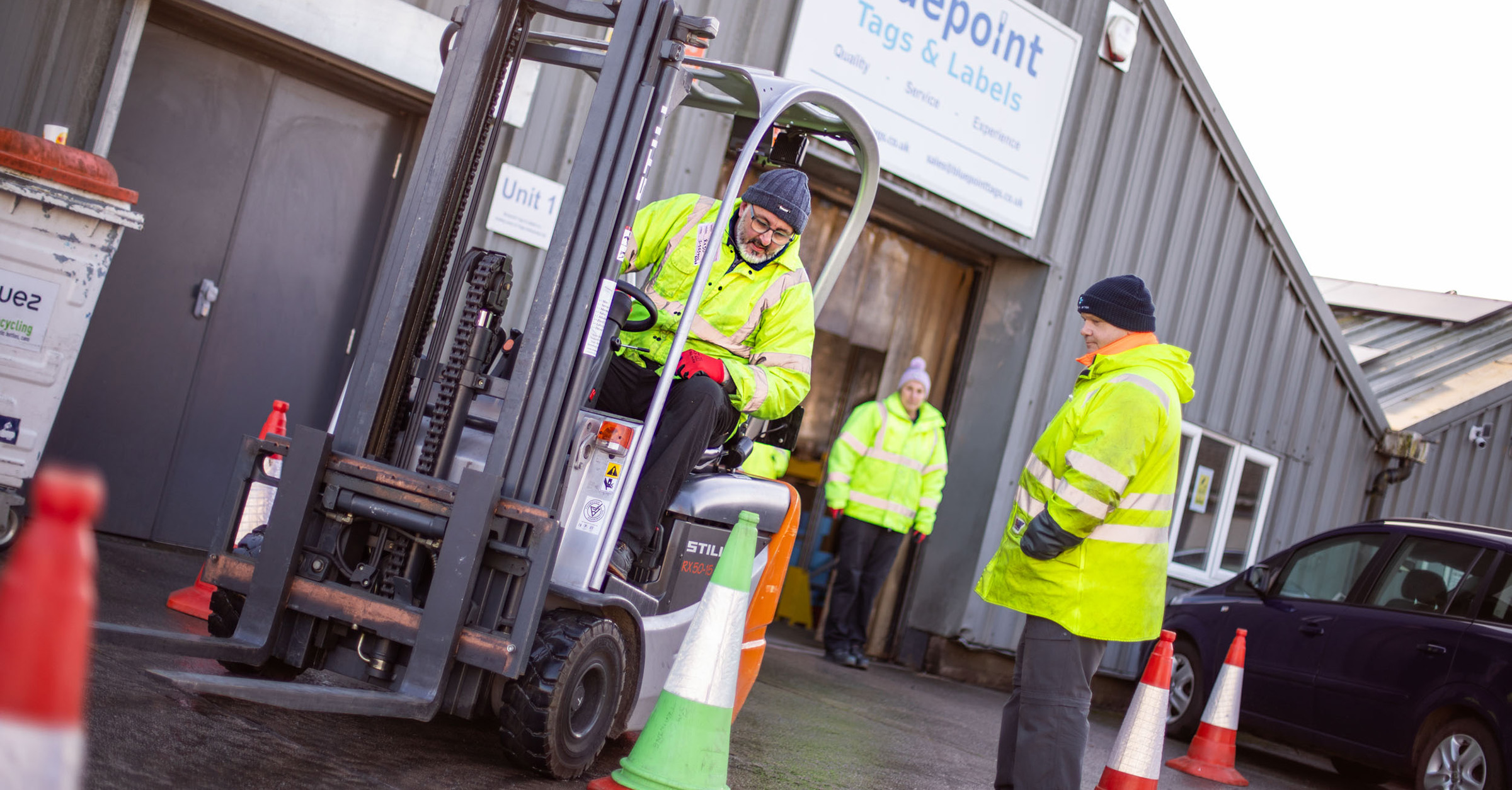
As well as reducing the risk of accidents and the downtime that accidents bring, there are several other benefits that we’ll enjoy as a result of training our team correctly...
- An improved safety culture – great training empowers our team to handle equipment responsibly, reducing risks to themselves and their colleagues not just on forklifts, but throughout our factory
- Enhanced efficiency – team members work more confidently, improving productivity and at the same time reducing wear and tear on our equipment due to improper use
- Lower costs – less accidents means less downtime and no drop in production
- Employee retention – we aim to make sure that we create a safe working environment for all our staff, and we’ll continue to invest in our team’s skills and training to ensure they stay safe, happy and valued in the workplace!
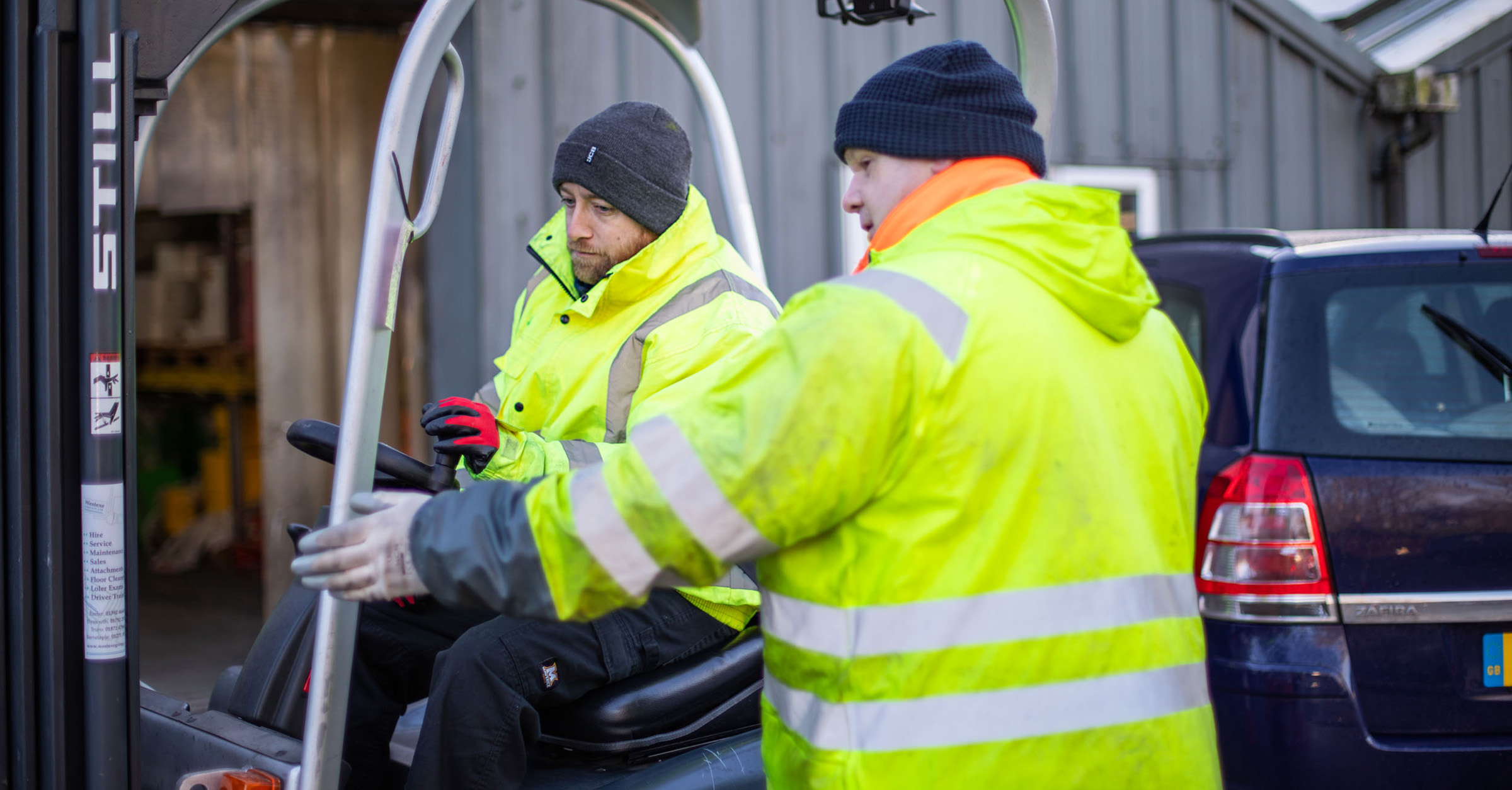
Iain Pringle, Director at Bluepoint, says:
“Congratulations to our team on doing their forklift training this week. Not only does this mean that everyone is trained correctly for better workplace safety, it also means that we have more available team members who can help move raw materials, so less production downtime and a faster turnaround for our customers.”
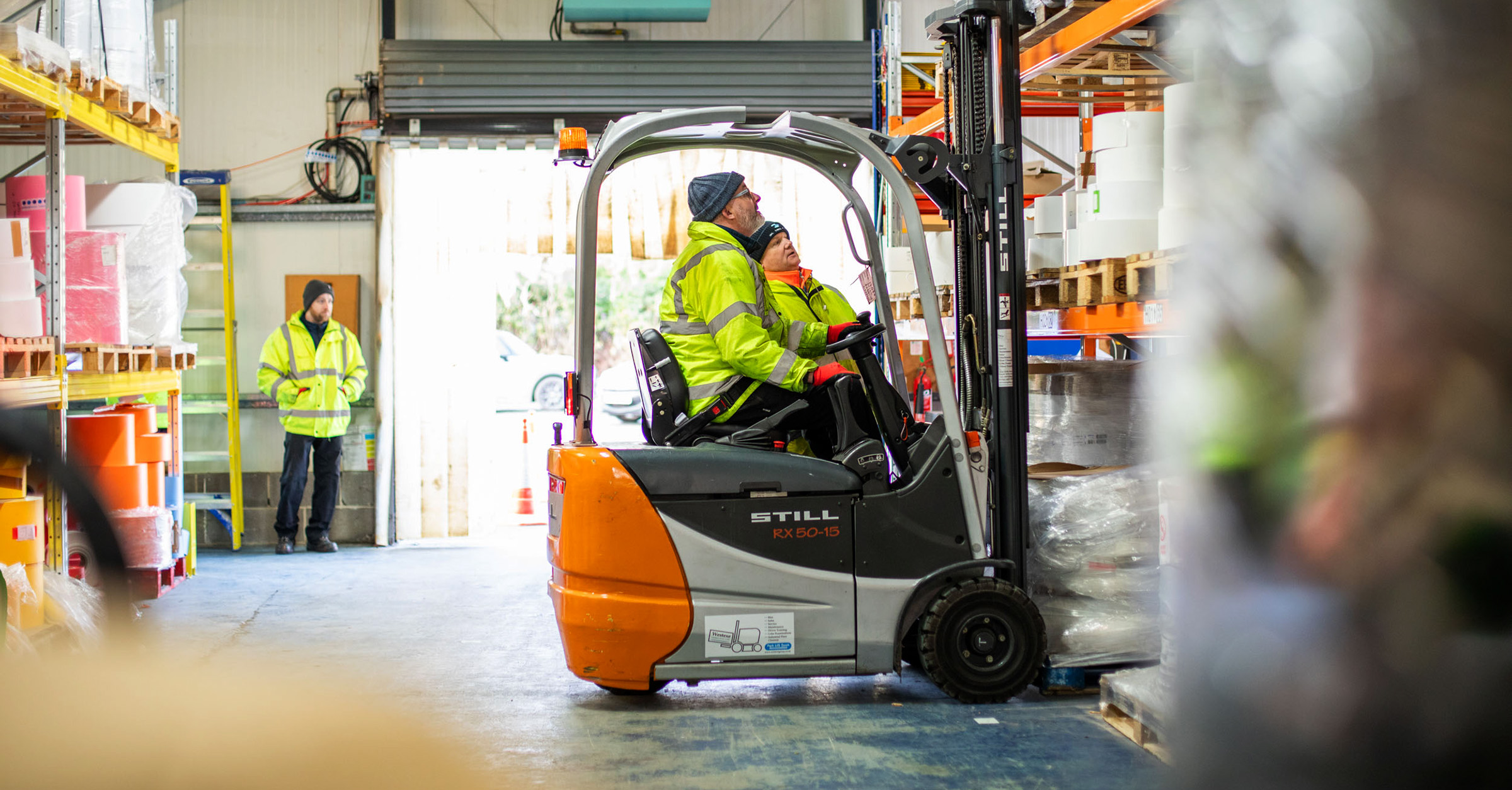
At Bluepoint, we love to do everything we can to make both a happy team and a highly efficient workspace – benefits that are clearly passed onto our customers who can enjoy the best products and the highest levels of good old-fashioned customer service. If you’d like to chat with one of our team about any of your label and printing requirements, drop James a line on 01392 927 030 or email him at [email protected].